Aseptic Process Development
Resources
- Knowledge Hub
- Knowledge Space
- Aseptic Processing
- Aseptic Processing Development
Aseptic Process Development
We are becoming increasingly reliant on drugs that need to be sterile and produced via aseptic processing. 3P has a wide range of standard aseptic fill-finish equipment at a range of scales. 3P are also recognised leaders in the supply of custom aseptic automation and associated isolators.
There are a range of pharmaceutical production applications which require special manufacturing processes called aseptic processing. They are often referred to as “fill-finish” and these production systems address specific risks associated with sterility through a range of cleaning, sterilisation, and isolation practices. Aseptic processing is normally associated with parenteral products which are injected and where terminal sterilisation of the end product is not practical. Aseptic processing is also necessary for a range of other pharmaceuticals, such as eye, nose or ear drops and sprays. This is due to the sensitive nature of these delicate mucus membranes.
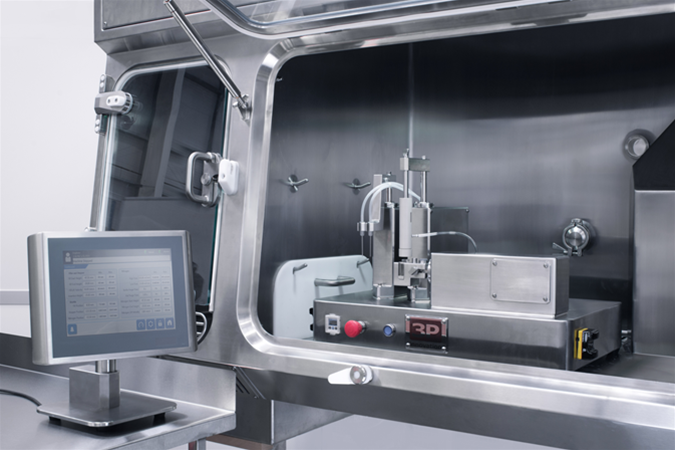
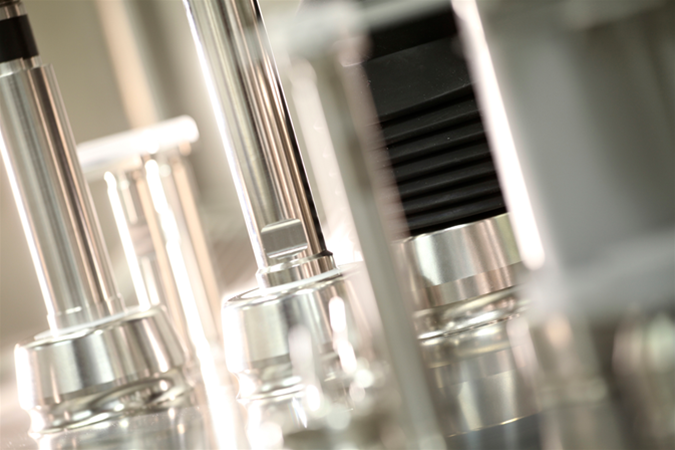
There are many vendors of “standard” fill-finish equipment including 3P. Aseptic processing is recognised as being particularly technically challenging. What therefore sets 3P apart is our ability to develop fully custom aseptic automation solutions. These are typically associated with novel pharmaceuticals, novel processes or novel delivery devices. 3P are also able to supply equipment to aseptically fill liquid and more unusually aseptically fill powders.
3P are able to support the total life-cycle of your novel aseptic product. We can supply equipment at a range of scales. Core to our philosophy at 3P is the ability to scale the same underlying process in response to the needs of our clients at the various stages of their drug or device development. We typically start with bench-top or lab-scale equipment to support their early pre-clinical or clinical studies. These can be converted to pilot-scale for later clinical trials. Finally, we can then convert this core technology to full scale production.
We use Quality by Design (QbD) principles to deliver robust aseptic processes to our clients. We will typically de-risk the core aseptic processes via the construction of functional prototypes which can be challenged ergonomically via wooden mock-up’s of the associated isolator technology. Prototyping enables significantly de-risking to take place. Using QbD terminology: Prototyping also provides an early understanding of the linkages between the product’s Critical Quality Attributes (CQA’s), the Critical Material Attributes (CMA’s) and the Critical Process Parameters (CPP’s). It is possible to explore the tolerances and sensitivities of the process in order to ensure that robust processes are used within any aseptic equipment.
Once the process and ergonomic aspects are de-risked, 3P are able to rapidly industrialise the aseptic process at a commensurate scale. Whether a client is looking to scale-up or scale-out 3P can then support with aseptic equipment to ramp-up capacity to match market demand. This is where the earlier efforts in defining a robust and scalable aseptic process will pay off.
Please refer to our case studies to see real world examples of our custom aseptic automation. These include assembly, filling, closing and testing of novel primary drug containers with liquids and powders.