Robotic Fill-Finish Cell
Pharma Equipment
- pharma equipment
- EXPLORE - Clinical scale
- Robotic Fill-Finish Cell
Robotic Fill-Finish Cell
Our fully automated robotic system is designed for aseptic liquid or powder filling of RTU containers.
Engineered from the ground up following the latest Annex 1 revision. With 100% level of quality inspection and advanced reject management, roboFIL™ minimises contamination, supporting a robust Contamination Control Strategy (CSS).
RTU product flexibility
Compatible with any RTU-based product- vials, syringes, cartridges, crimp caps, and press-fit caps - on a single platform. Our flexible vision-guided robot has removed the need for bowl feeders, enabling format changeover in minutes and introduction of new formats within hours.
Single source supply
Aseptic fill-finish can be highly complex. That's why both our isolator and process equipment are designed, manufactured, and integrated by 3P innovation. This single-source approach simplifies controls, service, maintenance and technical support.
Configure your aspetic fill-finish solution
Our roots in custom automation drive us to create tailored solutions for complex challenges. roboFIL™ features compact, modular chambers, offering configurable setups.
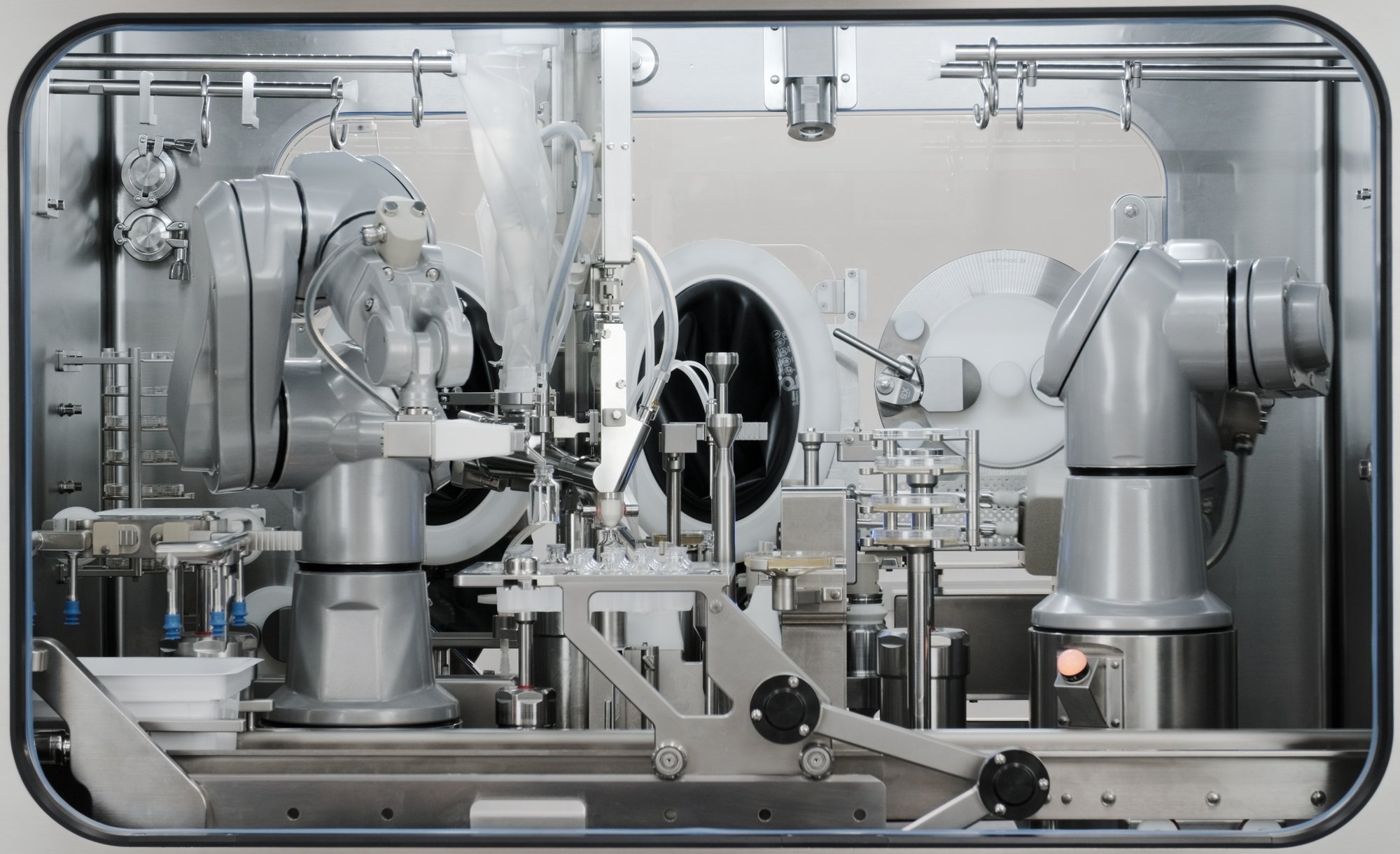
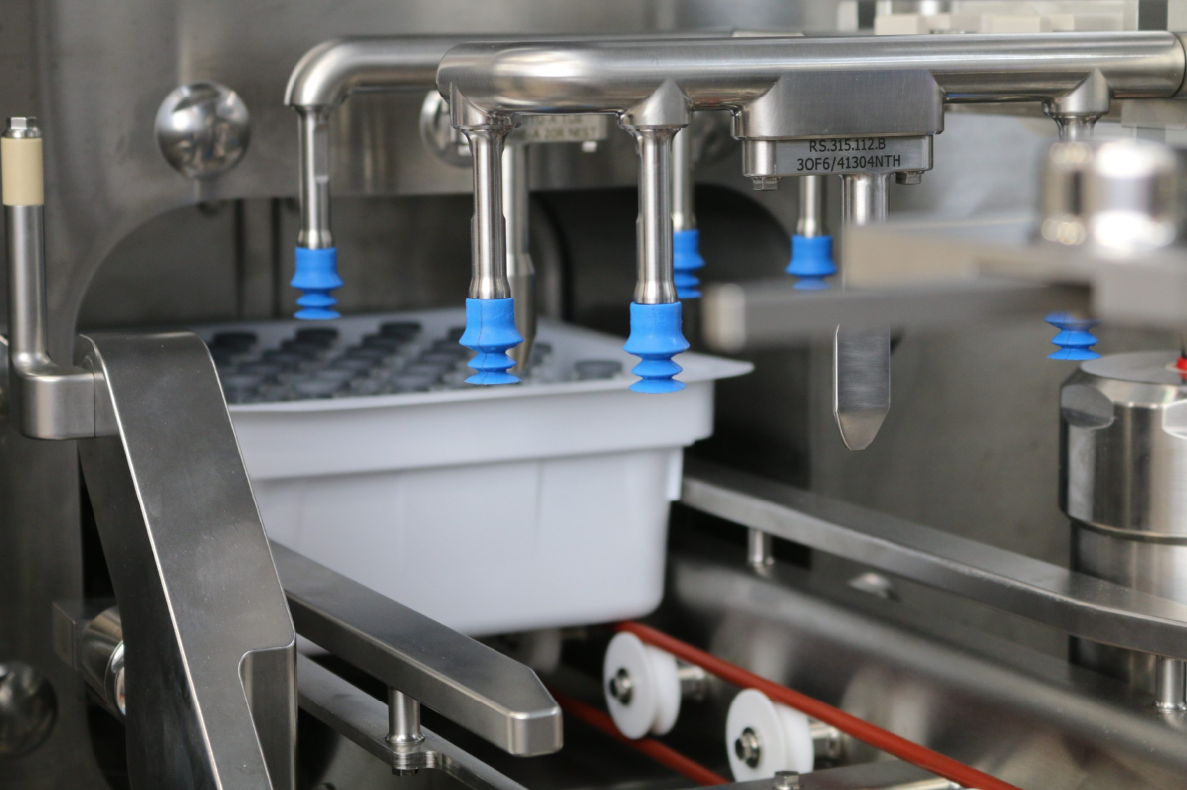
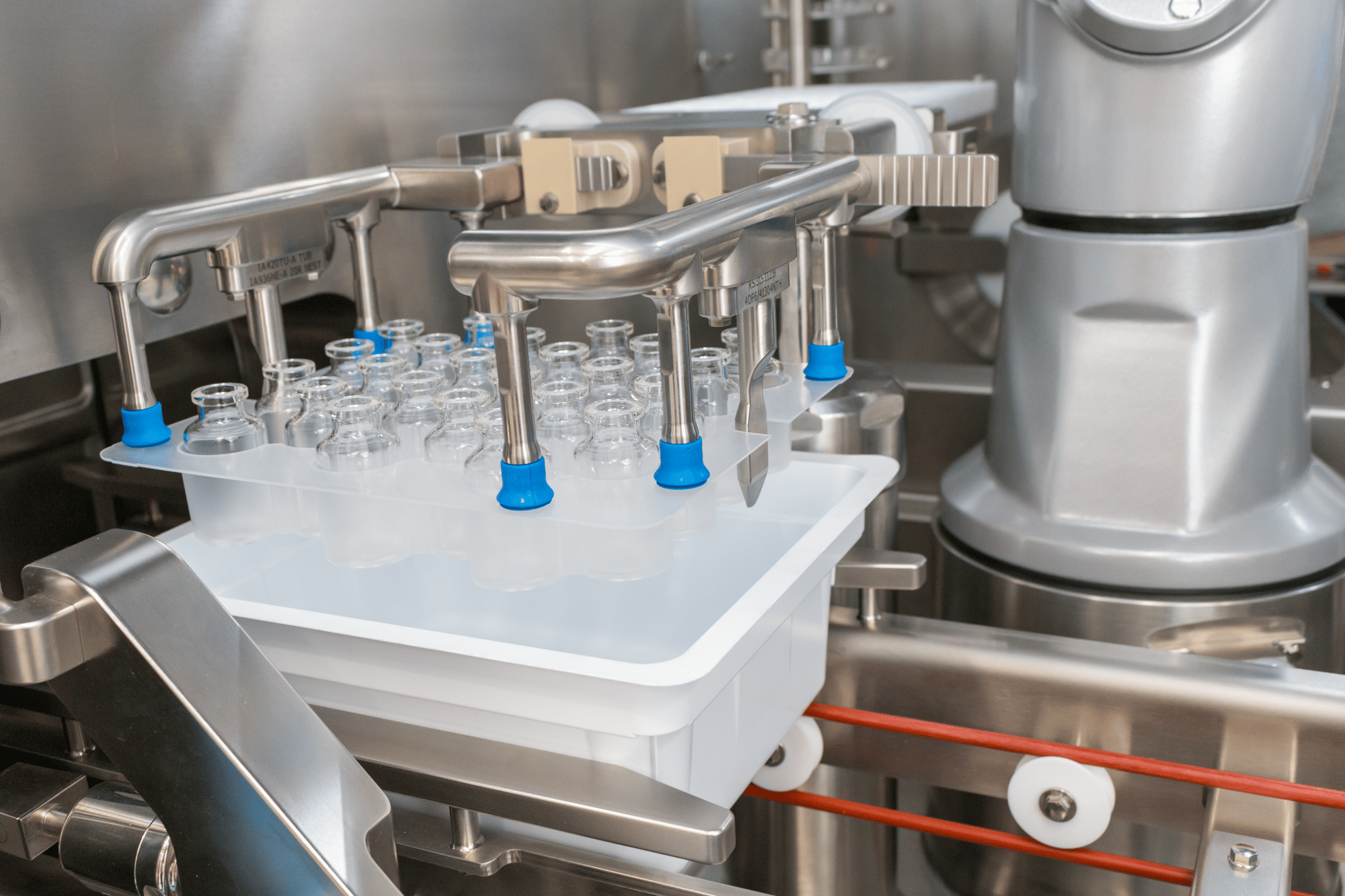
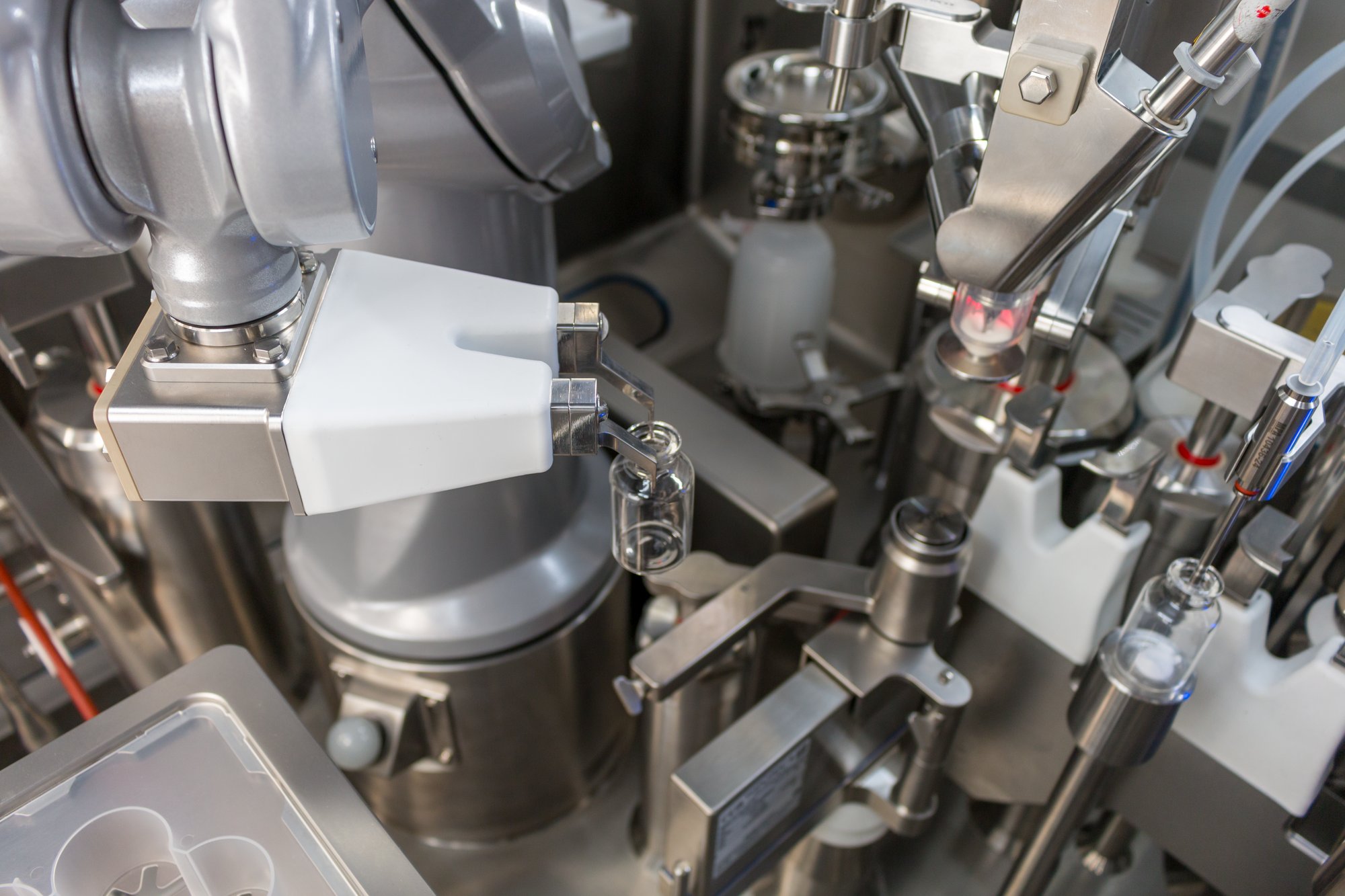
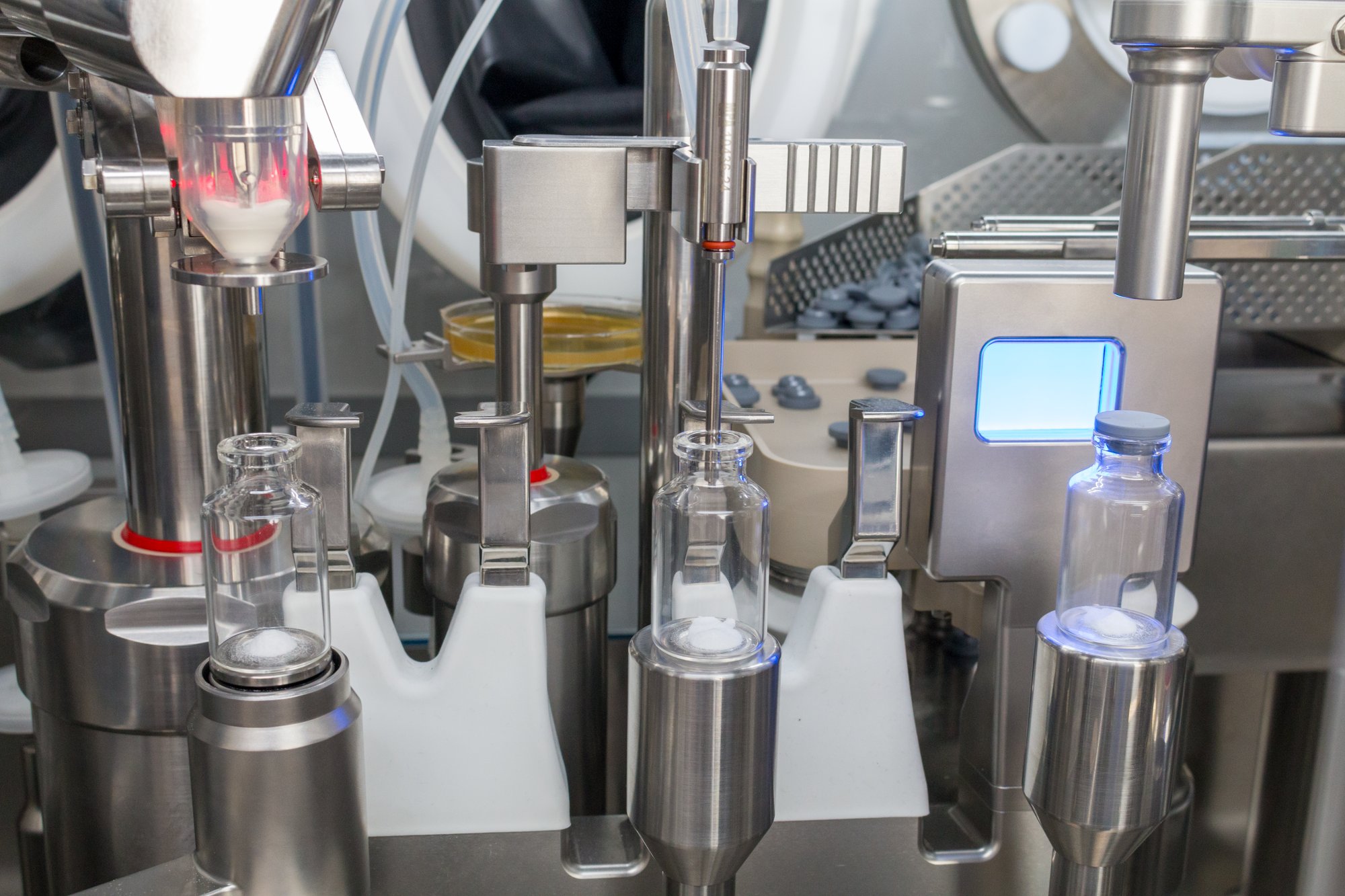
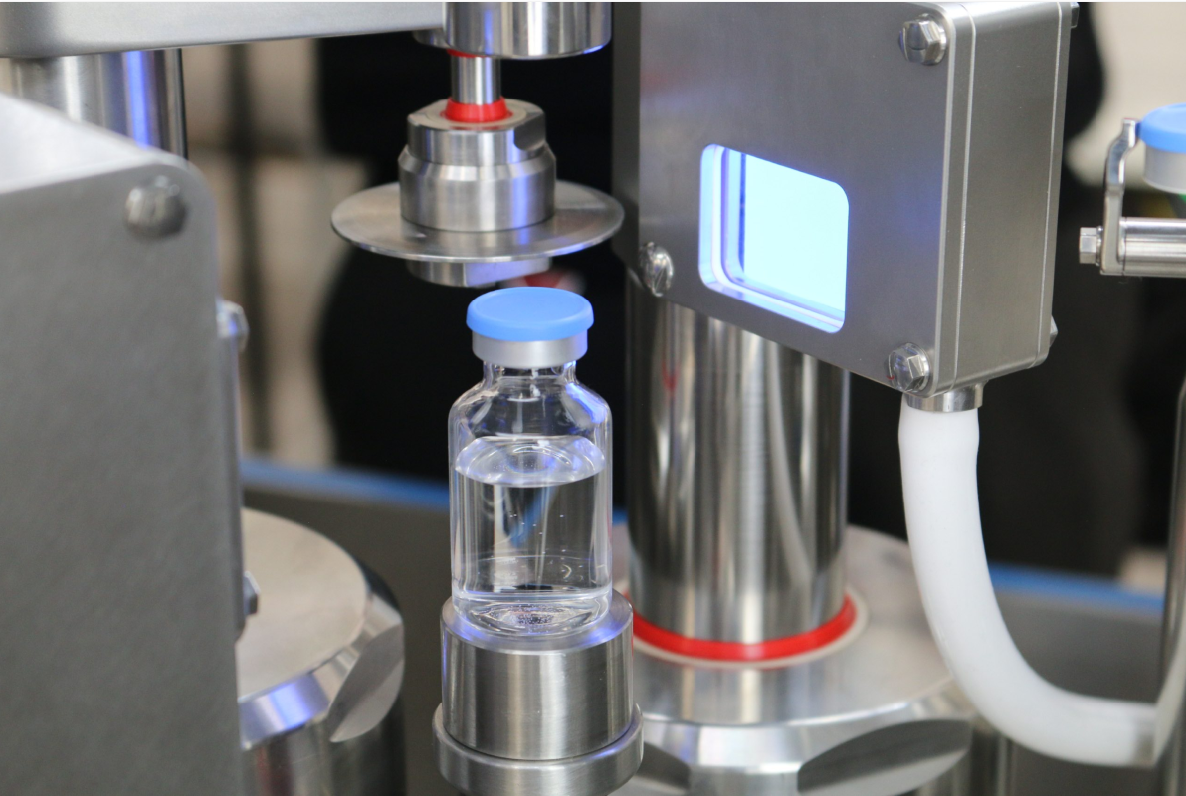
Get in touch...
Robotic Fill-Finish Cell
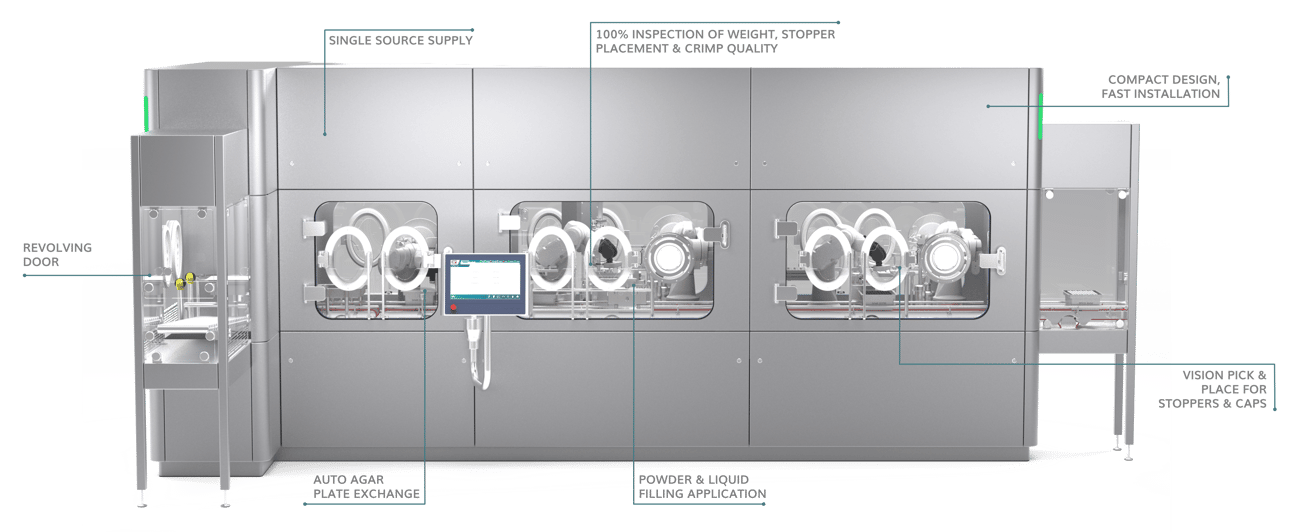
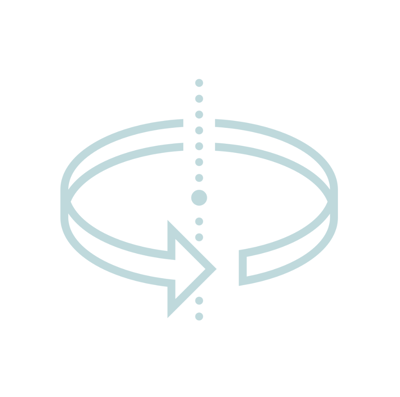
Revolving door. Increased throughput & reduced downtime.
Revolving door feature allows simultaneous loading and unloading of RTU tubs, increasing throughput and minimising downtime.
-1.png?width=300&height=300&name=Untitled%20design%20(6)-1.png)
Auto agar plate exchange. Elimination of routine interventions.
Automated gloveless management of agar plates eliminates routine interventions, with 24 hours runtime for settle plate and active air sampling locations.
.png?width=400&height=400&name=Untitled%20design%20(9).png)
Powder & liquid filling. Multi-format capable.
Capable of powder and/or liquid filling, making it suitable for reconstitution devices.
Incorporating our Fill2Weight technology for challenging powders.
-1.png?width=300&height=300&name=Untitled%20design%20(7)-1.png)
Compact & integrated design. Simplified installation.
roboFIL™ fits seamlessly into existing cleanrooms, with minimal integration, offering a smaller footprint and simpler, quicker set up.
.png?width=300&height=300&name=Untitled%20design%20(8).png)
Vision pick & place. Fast-format changeover.
Eliminates the need for bowl feeders, a vision-guided robot handles stoppers, press-fit and crimp caps, without the need for new change parts.
What's inside?
RoboFIL™ incorporates existing technology from our Discover Range. The integrated Liquid Fill-Finish pumping technology providing ultimate control and yield in liquid filling, whilst the Rotary Crimper provides consistent, precise crimping with compression force feedback. Looking for powder filling? Our Fill2Weight Gravimetric Powder Filler can be integrated into the system.
Aseptic powder filling
As demand grows for sterile, aseptically processed drugs, we offer a comprehensive selection of aseptic fill-finish equipment tailored for various production scales. We have a strong legacy in pharmaceutical powder micro-dosing and filling technologies, originally developed for the inhalation market. This expertise gives us a distinct advantage in the specialised field of aseptic powder fill-finish.
While most parenteral applications involve liquid fill-finish, there’s a growing need for powder fill-finish to address cold-chain challenges and enable sustained-release therapies. These powder formats are typically reconstituted with a diluent before administration, offering greater flexibility and reliability in a wide range of therapeutic settings. RoboFIL™ has been designed with this in mind, and is capable of aseptic powder, liquid, or combined filling, making it suitable for reconstitution devices.
Environmental cost of ownership (ECO)
Our aseptic fill-finish process is not just about maintaining product quality - it's also about reducing waste. When considering environmental impact, the main factors are energy, raw materials and waste. With traditional aseptic fill-finish lines, the biggest impact on the environment comes from cleaning. Preparing and decontaminating the equipment ready for use, cleaning and decontaminating vials, preparation and management of air suitable for the environment, washing equipment after use and dealing with effluent.
All activities are driven by the essential need to protect the drug product from contamination.
Our system offers several features that drive both economic and environmental benefits:
- Air recirculation technology: roboFIL™ reduces your energy consumption by drawing air in from the cleanroom and recirculating it.
- Waste reduction: No need to wash and sterilise RTU vials on the line. This eliminates the need for water or steam, drastically reducing energy consumption and waste generated at this stage in the process.
- A compact footprint with small filling chambers - roboFIL™ has been designed with energy consumption in mind. Less air volume means less air to manage, reducing energy consumption to operate and less VPHP required during the decontamination cycle.
- Automated fill-finish: Reduces the need for operators. Less PPE waste.
RoboFIL™ is a sustainable choice for drug developers looking to reduce costs and improve the environmental footprint of their manufacturing process.
Ongoing support from 3P innovation
Installation is just the start of your journey. Long-term reliability and robust machine performance are essential in maintaining the required output and quality of your product. That’s why our dedicated Customer Care team offers a comprehensive range of support services, backed by our Equipment Support Team (EST).
Partner with 3P innovation
3P innovation is the trusted partner for CDMOs and pharma industry leaders. We provide a fully integrated robotic fill-finish solution, which meets the highest standards of product quality, and regulatory compliance. When you work with us, you’re not just getting an equipment provider - you’re gaining a partner.
Book a discovery call today, to discuss your aseptic fill-finish requirements.
-
Lorem ipsum dolor amet aesthetic photo booth activated charcoal occupy iPhone schlitz squid. Everyday carry 3 wolf moon raw denim semiotics pok pok tattooed readymade bushwick. Humblebrag skateboard green juice mixtape polaroid ethical, messenger bag pitchfork sriracha hammock. Fam twee 3 wolf moon, authentic woke stumptown bespoke.
-
Lorem ipsum dolor amet aesthetic photo booth activated charcoal occupy iPhone schlitz squid. Everyday carry 3 wolf moon raw denim semiotics pok pok tattooed readymade bushwick. Humblebrag skateboard green juice mixtape polaroid ethical, messenger bag pitchfork sriracha hammock. Fam twee 3 wolf moon, authentic woke stumptown bespoke.
-
Lorem ipsum dolor amet aesthetic photo booth activated charcoal occupy iPhone schlitz squid. Everyday carry 3 wolf moon raw denim semiotics pok pok tattooed readymade bushwick. Humblebrag skateboard green juice mixtape polaroid ethical, messenger bag pitchfork sriracha hammock. Fam twee 3 wolf moon, authentic woke stumptown bespoke.