Designing custom, aseptic shadow trays
Custom Automation - Case Study
- Knowledge Hub
- Case Studies
- Designing custom, aseptic shadow trays for a leading pharmaceutical client
Designing custom, aseptic shadow trays for a leading pharmaceutical client
3P Custom automation is our traditional area of business, where we collaborate with customers to support product and process innovation across various industries.
To date, we have successfully delivered over 125 shadow trays to clients, across 6 unique projects. This case study focuses on our continued design and production of custom shadow trays for a leading pharmaceutical client.
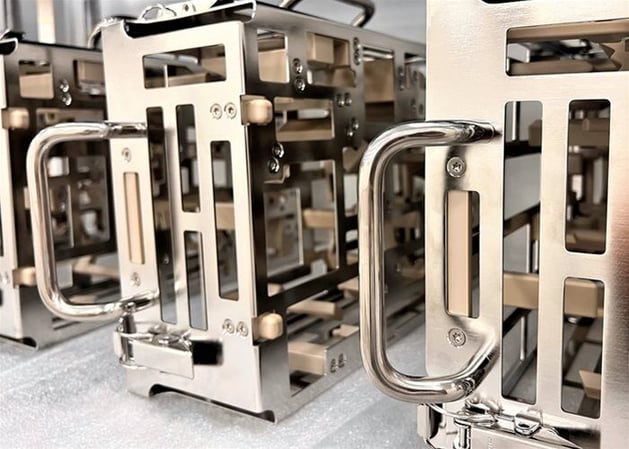
Shadow trays in the pharmaceutical industry
Shadow trays are critical to pharmaceutical manufacturing. Equipment used in this industry contains ‘product-contact parts’ - surfaces that come into contact with the drug product. The parts require cleaning and sterilising between uses to avoid product cross-contamination and to remove any presence of microorganisms or pathogens - a critical process in an industry where batch recall can inflict significant reputational damage. These parts must be sterilised away from the production equipment, and once removed will require secure transportation to and from a parts washer. Consisting of a base and removable lid, shadow trays enable the safe transfer, cleaning and sterilisation of these key product contact parts, ready for their next use.
Why 3P innovation?
One of 3P innovation’s clients previously relied on shadow trays manufactured by a separate supplier, however, they were unable to accommodate bespoke change requirements. With a proven history of delivering complex custom automation equipment for other key products, we had previously demonstrated high-end engineering competence to the client and were the obvious choice to re-design their shadow trays, whilst maintaining stringent quality standards.
How does 3P innovation design the highest-quality shadow trays for the client?
Ergonomic design
3P innovation’s shadow trays are ergonomically designed for aseptic unloading and custom-made with dimensions compatible with the washer/autoclave. The part unloading sequence is optimised through design iteration and prototype testing, preventing operator gloves from moving over any sterile parts.
Optimising the position & orientation of parts
3P innovation optimises the position and orientation of parts in the shadow tray to reduce the surface area hidden from the cleaning and sterilising media, ensuring minimal ‘shadows’ on the parts.
Parts are confined to a designated space using a mistake-proofing principle ensuring they cannot be loaded incorrectly; they are orientated such that they freely drain during washing - maximising exposure of critical faces and preventing the pooling of washing fluids. As such, parts are sterilised and washed in a specific and consistent way to provide total sterility assurance which is a critical requirement from the client’s perspective. If contamination is suspected, parts must be re-sterilised and investigated. A process deviation like this can be flagged by regulatory bodies during audits.
In addition to providing sterility assurance, the correct orientation of parts prevents unwanted movement during washing and handling. This is important as damage to parts can result in decreased product quality or machine running issues, which increases costs due to machine downtime. Any damage can also provide space for contamination to reside which can be more difficult to eliminate. To confirm the secure retention of change parts and reduce the risk of damage, the trays undergo a series of shake tests to ensure parts are not released from their designated positions (even when inverted).
The use of quality materials
High-grade stainless steel and PEEK are used in the construction of these trays to ensure a good surface finish and high product quality with a long working life. We also provide material traceability certificates for every tray, providing full transparency along with increased quality control.
Overview of our design process
Stage |
Details |
|
Identify parts to be contained within the shadow trays and determine the size constraints of the tray based on the washer/isolator dimensions and pickup method. |
|
Confirm the loading sequence from the shadow tray onto the machine. |
|
Generate 3D models of all parts to create a layout in CAD within a nominal ‘box’ to assess space feasibility. |
|
Design tray inserts to support change parts. |
|
Carry out a design review by conducting peer reviews against the specification to highlight potential improvements. This stage can occur multiple times, internally or with the customer. |
|
Create a basic prototype for ergonomic assessment only. Using non-electropolished metalwork of lower surface finish and rapid prototype inserts. |
|
Undergo ergonomic assessment within the mock-up processing environment to confirm that ergonomic needs are met. This assesses the physical process of trying to remove parts aseptically, ensuring that parts are easily loaded into trays and that they cannot be loaded incorrectly. The ergonomic assessment can lead to changes in orientation/position to facilitate easier loading/unloading or to ensure the sterilised parts remain aseptic by preventing contact with sources of contamination. |
|
Creation of an advanced prototype for washer coverage testing. Depending on design confidence this may be non-electropolished metalwork with machined acetal/temperature-resistant SLA inserts, or a production standard tray. |
|
Typically the customer carries this out by exposing the parts and tray to a UV dye and putting them through a ‘representative’ wash cycle to look for elements of the dye that remain. If dye is present at this stage the tray requires some re-design. |
|
|
|
FAT is a commercial activity that proves we have satisfied the customer’s needs, the requirements of which are determined by the client. In this case, there were five tests: 1) Is the loading/unloading sequence aseptically optimised? (2) Are change parts securely retained during a shake test at every angle? (3) Do trays fall under the threshold weight (<7kg), when populated? (4) Are the trays produced with approved materials for construction? (5) Is the surface finish of the trays acceptable? |
|
Install Qualification (IQ) Checks the physical dimensions, surface finishes and material certification. Operational Qualification (OQ) is through washer trial testing with the dye. Performance Qualification (PQ) - testing the operating window to ensure the process doesn't exceed acceptable limits when parameters are changed (e.g. washer cycle development - duration, temperature, loading patterns of parts in the washer, etc.). The IQ/OQ/PQ ensures the process is robust from a patient protection standpoint (i.e. ensuring the patient’s health is not at risk and no product recall is required, both of which are detrimental to the client). |
Through collaboration with the customer, 3P innovation has become the clients’ exclusive supplier for shadow trays, with over one hundred subsequent trays produced to fit their precise requirements. The customer-centric, flexible approach at 3P innovation has enabled the client to consistently meet challenging lead times.
If you’d like more information on our shadow tray services, or to learn about our custom automation division, please contact us at: enquiries@3Pinnovation.com.