Blogs
Knowledge Hub
- Knowledge Hub
- Blogs
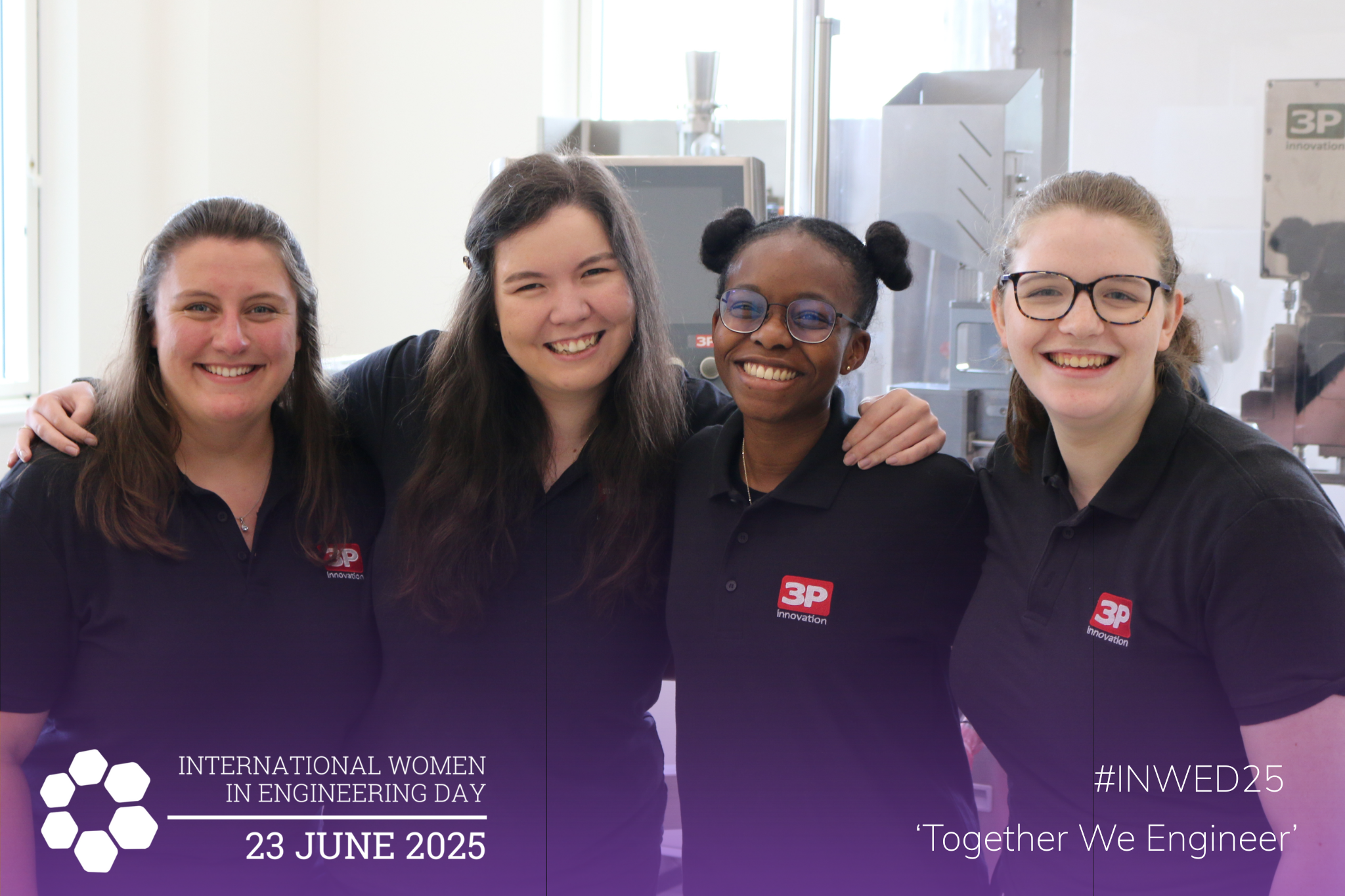
International Women in Engineering Day
Louise Fellows: 23 June 2025
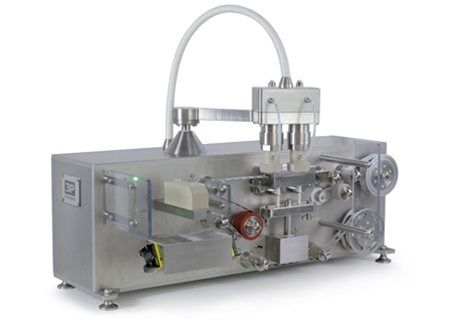
Film Sealing in Automation
Alex Jezequel: 16 June 2025